Na lavoura, quando um equipamento quebra, não é só dos custos de conserto que estamos falando. Também deve-se considerar os gastos acarretados pela parada não programada: mão de obra ociosa, deslocamento da equipe de reparos e, obviamente, o faturamento que deixa de existir. É claro que pode-se reparar o que for necessário e voltar à atividade. Mas, sem realizar a análise da causa raiz da falha, é bem provável que, em pouco tempo, você enfrente este problema novamente.
Ruídos, vibrações e falta de precisão dos equipamentos podem indicar problemas muito mais graves que aquele que está sendo percebido. É preciso investigar a causa raiz da falha e entender como evitá-la no futuro. Para isso, existe a Análise da Causa Raiz (ou RCA, sigla em inglês para Root Cause Analysis), que se baseia em encontrar, corrigir e documentar as falhas primárias, de modo a auxiliar na correta manutenção dos ativos.
Este método é importante, especialmente, para o setor de manutenção, uma vez que direciona os esforços das rotinas preditivas e preventivas. Neste artigo, selecionamos alguns métodos que podem ajudar os profissionais desta área a encontrarem a real causa raiz da falha e, assim, atuar com efetividade na prevenção de colapsos futuros. Acompanhe e entenda como fazer.
Causa raiz da falha: os principais métodos de análise
Embora gestores possam optar por diferentes métodos de análise, o objetivo deles é um só: encontrar a causa raiz do problema. E ela deve ser reduzida a uma só! Não importa se a forma de análise escolhida foi a Espinha de Peixe ou Os 5 Porquês ― que falaremos mais detalhadamente nos parágrafos abaixo ―, a metodologia deve ser certeira na detecção da falha inicial. Apenas com a certeza de lidar com o problema certo é que será possível encontrar a solução mais adequada.
Você irá perceber que muitas hipóteses serão levantadas durante a procura pela causa raiz da falha. Mas, é imprescindível que apenas uma delas seja apontada como a catalisadora dos eventos posteriores.
Técnica dos 5 porquês
Antes de começar, é bom ressaltar que o “5” citado é apenas uma referência. O número de “porquês” pode ir bem além deste que consta no título. O motivo é bem simples: encontrar a causa raiz da falha pode ser um trabalho bastante complexo e que envolve muitas variáveis.
A técnica consiste em fazer com que a falha apresentada sirva de base para questionamentos que, a medida que se aprofundam, revelam a causa raiz. Para ficar mais claro, imagine que o dente de uma engrenagem de um trator quebrou. Isso, claro, ocasionou a parada total do equipamento. Ao aplicar o método dos “5 porquês”, o raciocínio aplicado seria:
- Por que o dente quebrou? Porque haviam fendas na superfície metálica.
- Por que haviam essas fendas? Porque os micropittings que a causaram não foram detectados.
- Por que os micropittings surgiram? Porque o óleo lubrificante utilizado tinha ação antiespumante e fez com que o filme de proteção se rompesse, causando atrito entre as faces metálicas.
- Por que houve a compra equivocada do insumo? Porque não havia respaldo técnico na hora de realizar a cotação com os fornecedores.
- Por que faltou esse auxílio? Porque não há alinhamento entre os setores da empresa.
Leia também:
Com esse exemplo, você pôde perceber que houve uma série de falhas que levaram à quebra do dente da engrenagem:
- não houve um plano de manutenção preventiva que pudesse detectar o desgaste no dente e os micropittings não foram percebidos a tempo;
- o lubrificante utilizado era prejudicial à engrenagem, pois não houve apuração antes da compra;
- o processo de compra não teve respaldo técnico, portanto, negligenciou propriedades importantes do fluido.
Desta forma, um problema, literalmente, minúsculo como o micropitting (eles, comumente, possuem entre 10 e 20 µm de profundidade e largura, enquanto o comprimento varia de 25 a 100 µm) acarretou um efeito dominó que culminou na parada não programada do equipamento.
Entretanto, a causa raiz da falha é uma só: a falta de sincronia entre setores tão importantes para manter a competitividade da indústria.
Baixe gratuitamente:
Método Espinha de Peixe
Esta abordagem é mais visual. Embora seja parecida com a dos “5 Porquês”, trabalha um pouco mais na subcategorização dos problemas adjacentes. Para começar, você deve traçar uma linha horizontal (a “espinha do peixe”) e ramificações que partem deste esqueleto (as “costelas do peixe”). Cada ramificação corresponde a uma categoria que deve ser avaliada, sendo que estas também podem ser divididas em subcategorias.
Ainda considerando o exemplo anterior, onde há a quebra do dente da engrenagem do trator, ao utilizar o Método Espinha de Peixe (também conhecido como Diagrama de Ishikawa), a análise ocorreria da seguinte maneira:
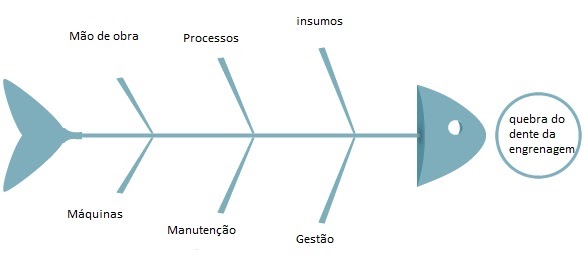
Nas ramificações, surgem as categorias que podem ter influência na causa raiz do problema. A cada subcategorização, é possível ver claramente quais segmentos podem ser descartados, quais inconformidades podem ser correlacionadas e quais são as verdadeiras causas raiz do problema.
O que fazer após identificar a causa raiz da falha
Diagnosticar a causa raiz da falha tem um papel fundamental para manter a competitividade do agronegócio. Apenas conhecendo os pontos de atenção das máquinas é que se podem traçar estratégias para mitigar os danos. Todavia, é preciso que as informações obtidas nas análises sirvam de base para evitar novos colapsos.
Para isso, atue seguindo estes 5 passos:
1. Identifique quais ações corretivas capazes de evitar a recorrência das falhas. Analise se essas atitudes reduziriam ou evitariam o colapso, caso tivessem sido implementadas previamente;
2. Categorize as ações corretivas em:
2.1 as que impediriam a recorrência com razoável certeza;
2.2 aquelas que estão dentro do seu controle;
2.3 que atendem as metas e objetivos;
2.4 as que não criam nem suscitam outros imprevistos.
3. Implemente as ações na causa raiz;
4. Acompanhe o desempenho dessas ações e garanta que estão atendendo as expectativas;
5. Detecte e aborde também as situações correlacionadas à causa raiz da falha.
Todas essas informações servem de base para a equipe de manutenção industrial. Em posse delas, o setor pode agir de modo a evitar novos problemas, gerar economia para a indústria e manter a disponibilidade dos ativos agrícolas, diminuindo até mesmo a sua depreciação.
Agora que você já sabe como identificar corretamente a causa raiz da falha, leia também sobre Nível de Criticidade: como definir prioridades. Continue acompanhando o Portal Inovação Industrial para mais novidades e artigos sobre a indústria.
Excelente!
muito bom mesmo interessante
Obrigado pelo interesse!